The emergence of IoT technology has been exemplarily beneficial for the manufacturing sector. Its integration in factories and workshops has led to the rise of some out-of-the-box features that were not possible with the legacy SCADA and PLC systems.
The term “Industrial IoT” or “IoT” is hence used by many that showcase the brilliance of this technology in an industrial setup. It is the future of manufacturing that can optimize on-floor operations and enable a machine to machine interaction to create a connected and automated environment within an industry.
How be it, before you implement this technology to garner the capabilities of M2M synchronization and automation, you must first leverage it for machine monitoring. IoT-based machine monitoring systems are much easier to deploy in a machine-driven environment and can help you obtain a high return on investment and that too in a payback period of a few months.
Moreover, small-scale industries that are looking for a breakthrough innovation can easily implement IoT machine monitoring systems to compete with already established manufacturing giants.
Not sure what machine monitoring is?
Let’s understand this concept.
What is Machine Monitoring?
Machine monitoring is a systematic process of gathering real-time data and insights from industrial machinery. It involves the utilization of sensors, connectivity, and data analytics to monitor the performance, health, and productivity of the machines.
By continuously tracking key parameters such as operational status, energy consumption, and maintenance requirements, it enables you to do proactive maintenance, reduces downtime, and optimizes overall operational efficiency.
It empowers your businesses to make data-driven decisions, identify bottlenecks, and improve productivity. With machine monitoring, organizations can harness the power of technology to maximize equipment utilization, extend lifespan, and drive continuous improvement in their industrial processes.
How Does IoT Help in Machine Monitoring?
IoT means a network of interconnected devices that share information. In a manufacturing facility or workshop, the IoT makes use of web-enabled sensors and devices that are installed on every machine present on a factory floor.
Essential data about these machines is collected via sensors embedded in/on them and is shared with a centralized platform in real time that processes it into useful information. Machine operators and workplace supervisors can use this information to make smart decisions to boost the efficiency of their production lines.
While there are several benefits of using machine monitoring in a factory, the final result in most cases is the same. These systems help companies to reduce their operational costs and boost their production rate while maintaining optimum plant efficiency.
Manufacturing Before IoT
Before the advent of IoT, there was no possible way to identify the status and condition of machines. Costly manual inspection operations were required to supervise the condition of a production line. Moreover, there wasn’t any proper way to identify problems that resulted in machine breakdown and unwanted downtime.
Even though the Industrial Revolution 3.0 left SCADA and PLC systems for companies to monitor the condition and performance of their facilities, they had several complications related to inflexibility and scalability. They are ineffective outside the fence applications and are quite rigid due to their complex wired structure.
Furthermore, these systems are purely reactive and do not facilitate machine-to-machine interaction which is quite essential for modern-day manufacturing setup. This communication disconnects among machines restricted operators and supervisors from proactively managing their equipment and reducing the downtime of their production lines.
But the implementation of IoT technology has helped workshops and companies to overcome these issues and garner benefits from real-time machine monitoring systems. The data collected from end devices installed on machines can be processed and used to identify bottlenecks and improve the efficiency of the facility.
Applicability of IoT-based Machine Monitoring in Manufacturing
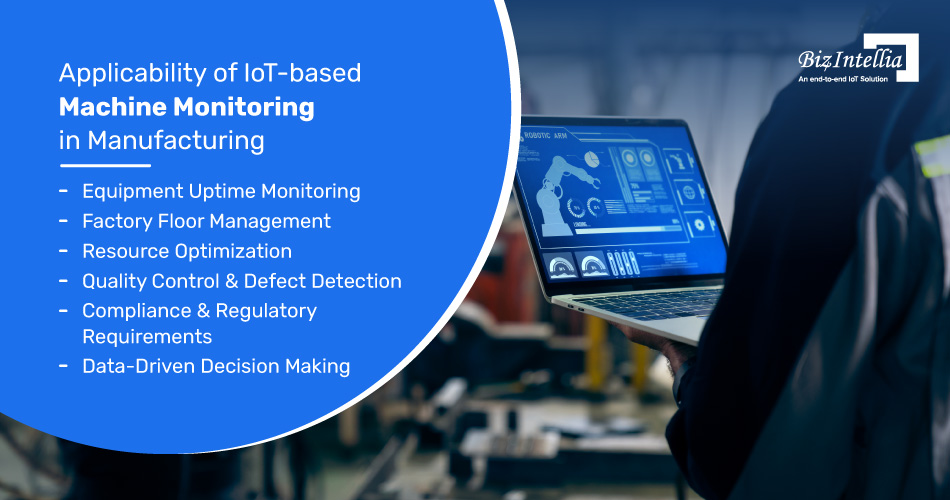
Below are some of the most intriguing applications of IoT-based machine monitoring.
1) Equipment Uptime Monitoring
Companies want their plants to operate effectively and in a streamlined process. However, maintaining a lean manufacturing approach is no easy feat to achieve.
They often face unwanted component breakdowns and machine malfunctions that restrict them to keep their production line running.
With IoT machine monitoring, companies can track when the machine was running and when it was not. They can gain real-time alerts about the machine going down and can hence take proactive measures to reduce downtime.
Moreover, by analyzing the data collected about the machine being in uptime and downtime, companies can identify reasons that result in equipment failures.
2) Factory Floor Management
Many different factors contribute to determining the efficiency of a factory or workshop. Essentially, since most of the tasks are conducted by machines, equipment, and industrial assets; they grasp a major chunk in determining efficiency.
By processing the data from monitoring systems, machine handlers can determine inadequacies and inefficiencies that restrict machines from operating with the utmost efficiency.
For example, with energy monitoring solutions, companies can monitor the amount of energy consumed by the machines and take effective measures to control their power quality events.
The real-time energy consumption insights allow companies to do so and help them to proactively manage power utilization, which in turn helps them to improve the efficiency of their plant.
3) Resource Optimization
Machines consume more resources when their condition is not up to the mark.
In this case, the machines will not only utilize more resources but will also waste the raw materials. Companies hence need to keep an eye on the performance of their assets along with the amount the resources that they utilize.
By using industrial IoT monitoring systems, parameters like temperature, pressure, noise, vibrations, etc. can be monitored to reflect the condition of the industrial apparatus.
Moreover, these parameters will help companies to identify the volume of resources consumed by the machines. They can hence limit the utilization of resources like fuel, electricity, lubricant, coolant, etc., manage proper stock levels, and decrease wastage.
4) Quality Control and Defect Detection
Ensuring product quality and detecting defects in real time is crucial for maintaining customer satisfaction and minimizing rework or product recalls.
Machine monitoring industrial IoT solutions can capture and analyze data related to product quality parameters, such as dimensions, weight, or visual appearance. By correlating machine performance with product quality metrics, companies can identify correlations between machine conditions and product defects.
Real-time alerts and automated inspections enable swift detection of deviations or anomalies, allowing prompt corrective actions and preventing the production of defective or substandard products. This approach enhances quality control, reduces waste, and safeguards brand reputation.
5) Compliance and Regulatory Requirements
Meeting industry-specific compliance standards and regulatory requirements is essential for ensuring operational safety, environmental sustainability, and adherence to legal obligations.
Machine monitoring solutions help companies monitor and analyze data related to compliance parameters, such as emission levels, noise, or safety alerts.
Real-time alerts and continuous monitoring enable prompt action in case of non-compliance, ensuring adherence to regulatory standards. By maintaining a record of machine performance data and compliance events, companies can generate accurate reports and demonstrate compliance during audits.
This helps your business to proactively compliance management, minimizes the risk of penalties, and promotes a safe and sustainable working environment.
6) Data-Driven Decision Making
In the era of Industry 4.0, data is a valuable asset for making informed business decisions. Machine monitoring generates a wealth of data that can be analyzed to gain valuable insights.
By leveraging advanced analytics and data visualization tools, companies can extract actionable intelligence from machine monitoring data. This enables them to identify patterns, trends, and correlations that can drive strategic decision-making.
Whether it's optimizing production processes, planning for capacity expansion, or identifying areas for cost savings, machine monitoring empowers companies with data-driven decision-making capabilities.
Steps to take After Implementing Machine Monitoring Systems
It’s quite prevalent and clear now that machine monitoring is the first yet rudimental step for industrial IoT implementation.
After successfully implementing the monitoring systems, a company can then use analytics tools along with AI and automation techniques to boost the effectiveness of their equipment and plant even further.
The extent to which a company can benefit from the implementation of IoT technology is immense.
Machine monitoring solutions can be the first step for the IIoT implementation that a company can take to achieve operational excellence.